The Evolution of Welding:
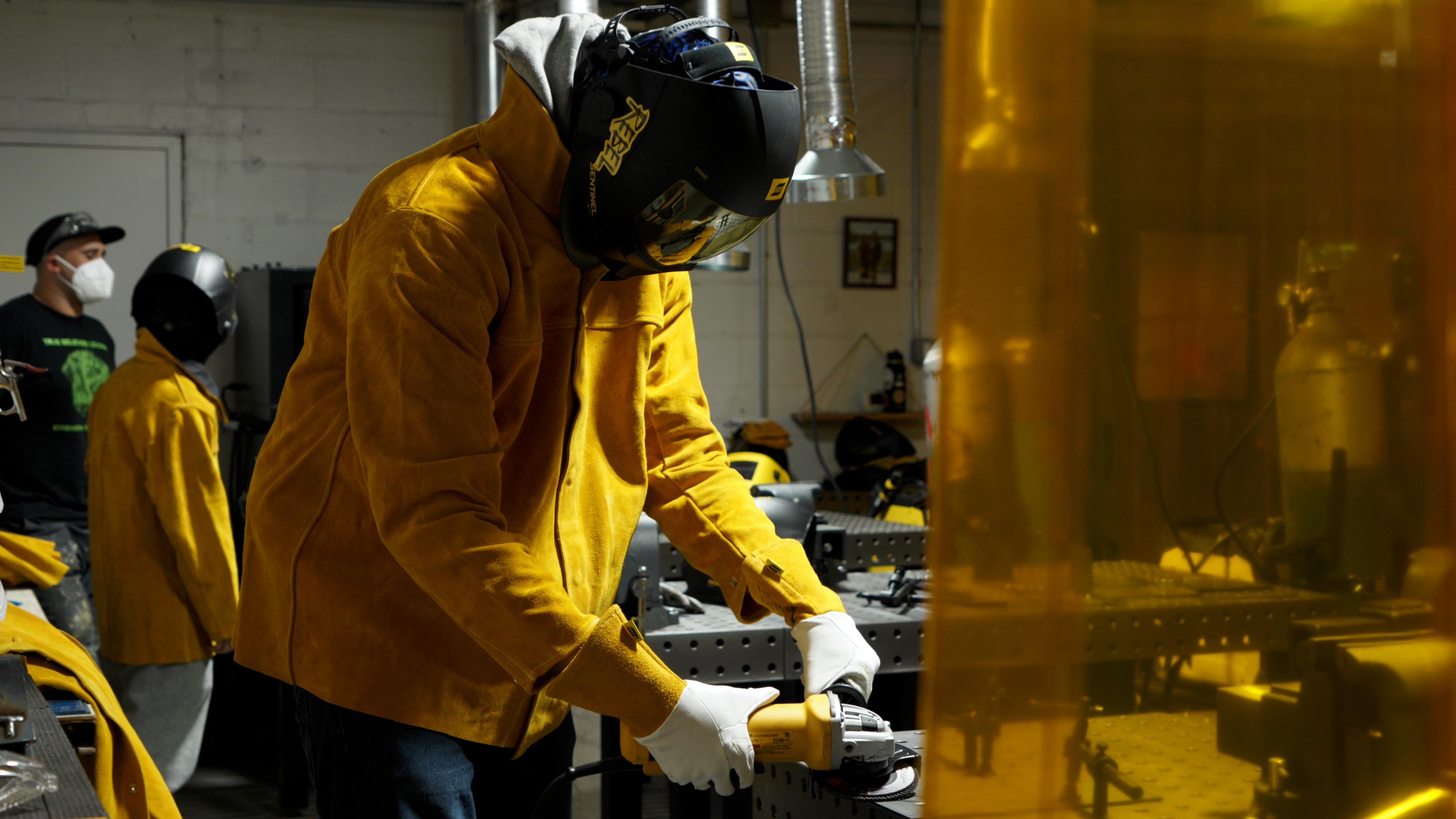
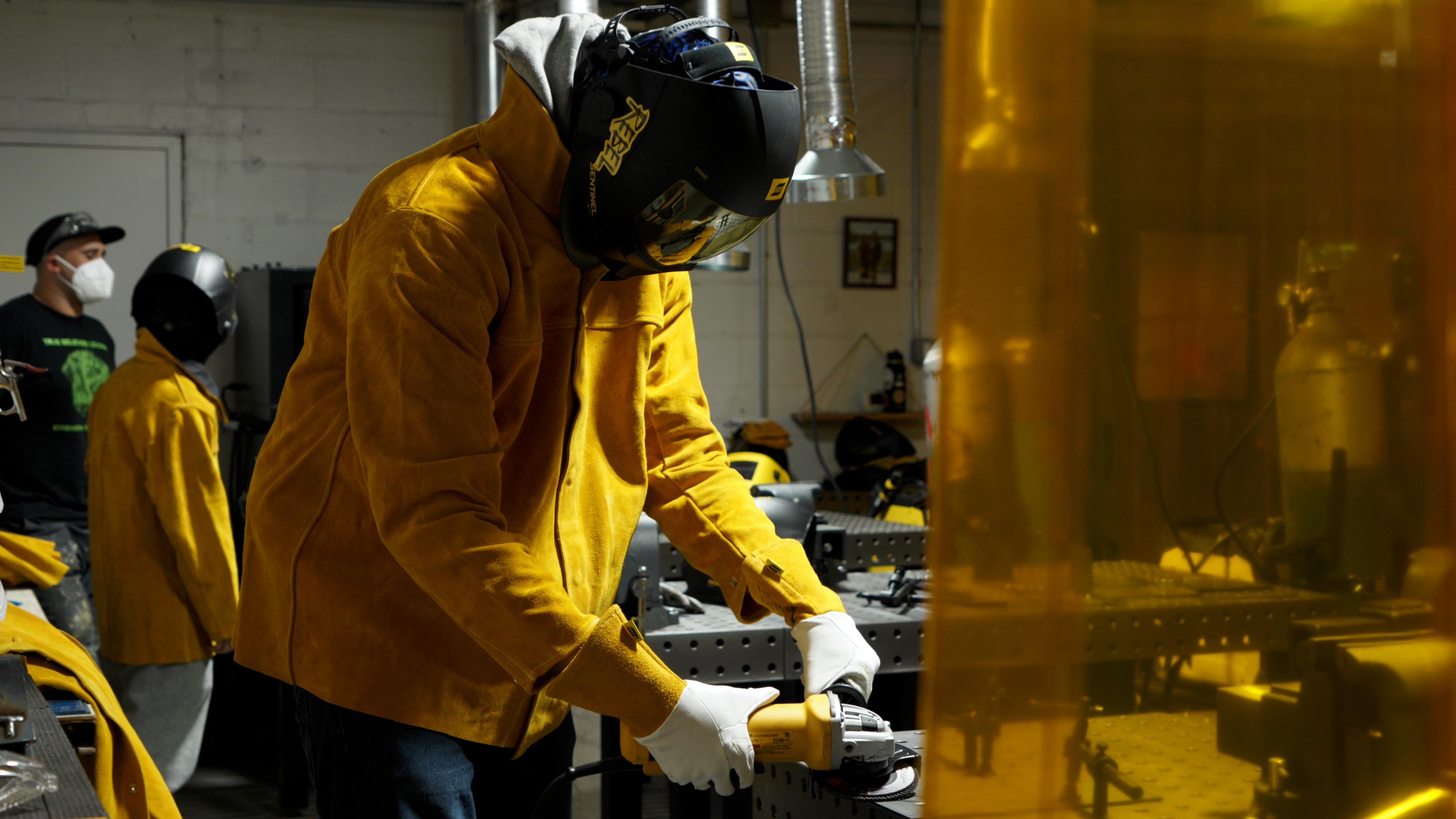
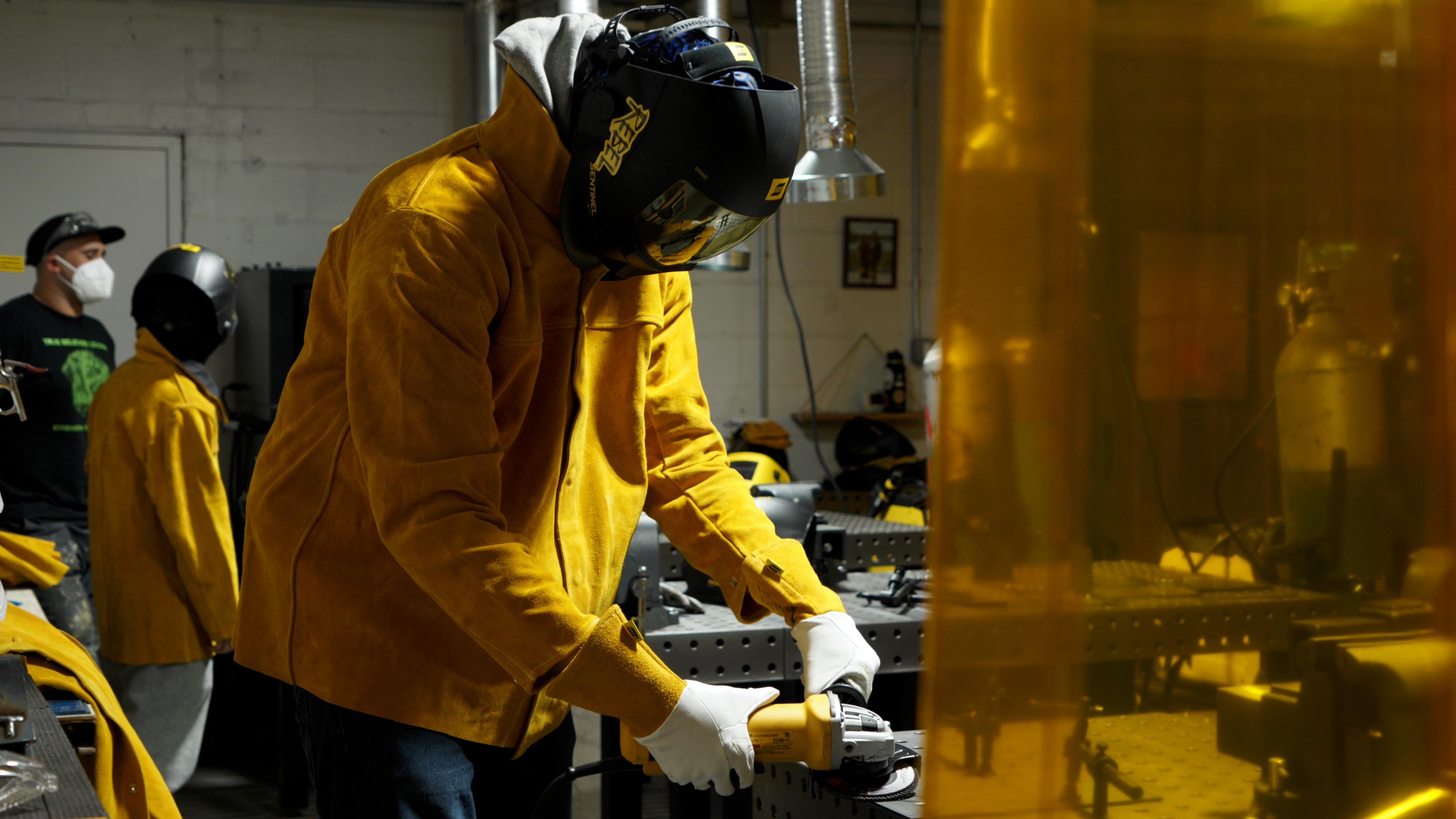
Welding has long been the backbone of manufacturing, construction, and many other industries. Traditionally characterized by intense physical labor, precise skill, and manual tools, the field is undergoing a significant transformation.
The modern welder now finds themselves at the intersection of craftsmanship and advanced technology. This evolution is reshaping the industry, making it imperative for newcomers to not only master the art of welding but also become proficient in the latest technological advancements.
Waterjet cutting technology
Integration of Technology in Welding
The incorporation of technology into welding workflows has revolutionized how projects are executed. Water jet cutting, plasma cutting, and advanced manufacturing equipment have enhanced precision, efficiency, and safety.
Water jet cutters, for example, use high-pressure water mixed with abrasives to cut through materials, offering a level of versatility and precision that traditional methods struggle to match.
Similarly, plasma cutting systems utilize ionized gas to cut through electrically conductive materials, providing faster and cleaner cuts than traditional torches.
Plasma cutting technology
Moreover, the advent of automation and robotics in welding has not only increased productivity but also reduced human error, leading to higher-quality outputs. Robotic arms, programmed to perform repetitive tasks, ensure consistent welds and allow human welders to focus on more complex and intricate work.
The Role of Software and Analytics
Software and analytics play a crucial role in modern welding. From design to execution, software tools help in creating detailed plans, simulations, and adjustments before any physical work begins. This pre-emptive planning significantly reduces waste and improves project outcomes. Additionally, analytics enable the monitoring of equipment performance and the prediction of maintenance needs, minimizing downtime and extending the lifespan of valuable machinery.
Empowering Newcomers through Knowledge and Adaptation
For newcomers to the welding industry, embracing these technological advancements is crucial for success. Understanding and leveraging tools like CAD (Computer-Aided Design) software for planning, or mastering the use of CNC (Computer Numerical Control) machines for precise cutting, can set a new welder apart. Educational institutions and training programs are increasingly incorporating these technologies into their curricula, reflecting the industry's evolving needs.
The future of welding lies in a skilled workforce that is not only proficient in manual welding techniques but is also knowledgeable about advanced manufacturing equipment, software, and analytics. Continuous learning and adaptation to new technologies will be the key to excelling in this transforming field.
Applying Technology to a Pipeline of Work
Across the diverse industries reliant on welding, the integration of technology is becoming essential. Advanced equipment and software enhance weld quality, optimize processes, and improve safety. Embracing these technological advancements empowers welders to work more efficiently, produce superior results, and expand their career opportunities across all sectors of the welding industry.
Forging Ahead
The welding industry is at a pivotal point in its evolution, with technology playing a central role in its future direction. For those entering the field, the opportunities are vast, but so is the need for a new kind of expertise.
By becoming proficient in both the art of welding and the technology that now drives it, welders can ensure their place in the future of manufacturing, construction, and beyond. The modern welder is no longer just a craftsman but a technologically savvy professional, poised to meet the challenges of the 21st century.
Interested in learning more about our programs?
Welding has long been the backbone of manufacturing, construction, and many other industries. Traditionally characterized by intense physical labor, precise skill, and manual tools, the field is undergoing a significant transformation.
The modern welder now finds themselves at the intersection of craftsmanship and advanced technology. This evolution is reshaping the industry, making it imperative for newcomers to not only master the art of welding but also become proficient in the latest technological advancements.
Waterjet cutting technology
Integration of Technology in Welding
The incorporation of technology into welding workflows has revolutionized how projects are executed. Water jet cutting, plasma cutting, and advanced manufacturing equipment have enhanced precision, efficiency, and safety.
Water jet cutters, for example, use high-pressure water mixed with abrasives to cut through materials, offering a level of versatility and precision that traditional methods struggle to match.
Similarly, plasma cutting systems utilize ionized gas to cut through electrically conductive materials, providing faster and cleaner cuts than traditional torches.
Plasma cutting technology
Moreover, the advent of automation and robotics in welding has not only increased productivity but also reduced human error, leading to higher-quality outputs. Robotic arms, programmed to perform repetitive tasks, ensure consistent welds and allow human welders to focus on more complex and intricate work.
The Role of Software and Analytics
Software and analytics play a crucial role in modern welding. From design to execution, software tools help in creating detailed plans, simulations, and adjustments before any physical work begins. This pre-emptive planning significantly reduces waste and improves project outcomes. Additionally, analytics enable the monitoring of equipment performance and the prediction of maintenance needs, minimizing downtime and extending the lifespan of valuable machinery.
Empowering Newcomers through Knowledge and Adaptation
For newcomers to the welding industry, embracing these technological advancements is crucial for success. Understanding and leveraging tools like CAD (Computer-Aided Design) software for planning, or mastering the use of CNC (Computer Numerical Control) machines for precise cutting, can set a new welder apart. Educational institutions and training programs are increasingly incorporating these technologies into their curricula, reflecting the industry's evolving needs.
The future of welding lies in a skilled workforce that is not only proficient in manual welding techniques but is also knowledgeable about advanced manufacturing equipment, software, and analytics. Continuous learning and adaptation to new technologies will be the key to excelling in this transforming field.
Applying Technology to a Pipeline of Work
Across the diverse industries reliant on welding, the integration of technology is becoming essential. Advanced equipment and software enhance weld quality, optimize processes, and improve safety. Embracing these technological advancements empowers welders to work more efficiently, produce superior results, and expand their career opportunities across all sectors of the welding industry.
Forging Ahead
The welding industry is at a pivotal point in its evolution, with technology playing a central role in its future direction. For those entering the field, the opportunities are vast, but so is the need for a new kind of expertise.
By becoming proficient in both the art of welding and the technology that now drives it, welders can ensure their place in the future of manufacturing, construction, and beyond. The modern welder is no longer just a craftsman but a technologically savvy professional, poised to meet the challenges of the 21st century.
Interested in learning more about our programs?
Welding has long been the backbone of manufacturing, construction, and many other industries. Traditionally characterized by intense physical labor, precise skill, and manual tools, the field is undergoing a significant transformation.
The modern welder now finds themselves at the intersection of craftsmanship and advanced technology. This evolution is reshaping the industry, making it imperative for newcomers to not only master the art of welding but also become proficient in the latest technological advancements.
Waterjet cutting technology
Integration of Technology in Welding
The incorporation of technology into welding workflows has revolutionized how projects are executed. Water jet cutting, plasma cutting, and advanced manufacturing equipment have enhanced precision, efficiency, and safety.
Water jet cutters, for example, use high-pressure water mixed with abrasives to cut through materials, offering a level of versatility and precision that traditional methods struggle to match.
Similarly, plasma cutting systems utilize ionized gas to cut through electrically conductive materials, providing faster and cleaner cuts than traditional torches.
Plasma cutting technology
Moreover, the advent of automation and robotics in welding has not only increased productivity but also reduced human error, leading to higher-quality outputs. Robotic arms, programmed to perform repetitive tasks, ensure consistent welds and allow human welders to focus on more complex and intricate work.
The Role of Software and Analytics
Software and analytics play a crucial role in modern welding. From design to execution, software tools help in creating detailed plans, simulations, and adjustments before any physical work begins. This pre-emptive planning significantly reduces waste and improves project outcomes. Additionally, analytics enable the monitoring of equipment performance and the prediction of maintenance needs, minimizing downtime and extending the lifespan of valuable machinery.
Empowering Newcomers through Knowledge and Adaptation
For newcomers to the welding industry, embracing these technological advancements is crucial for success. Understanding and leveraging tools like CAD (Computer-Aided Design) software for planning, or mastering the use of CNC (Computer Numerical Control) machines for precise cutting, can set a new welder apart. Educational institutions and training programs are increasingly incorporating these technologies into their curricula, reflecting the industry's evolving needs.
The future of welding lies in a skilled workforce that is not only proficient in manual welding techniques but is also knowledgeable about advanced manufacturing equipment, software, and analytics. Continuous learning and adaptation to new technologies will be the key to excelling in this transforming field.
Applying Technology to a Pipeline of Work
Across the diverse industries reliant on welding, the integration of technology is becoming essential. Advanced equipment and software enhance weld quality, optimize processes, and improve safety. Embracing these technological advancements empowers welders to work more efficiently, produce superior results, and expand their career opportunities across all sectors of the welding industry.
Forging Ahead
The welding industry is at a pivotal point in its evolution, with technology playing a central role in its future direction. For those entering the field, the opportunities are vast, but so is the need for a new kind of expertise.
By becoming proficient in both the art of welding and the technology that now drives it, welders can ensure their place in the future of manufacturing, construction, and beyond. The modern welder is no longer just a craftsman but a technologically savvy professional, poised to meet the challenges of the 21st century.
Interested in learning more about our programs?
Category
Industry
Read More
Igniting the future generation of Welders
Stay up to date
Igniting the future generation of Welders
Stay up to date
Igniting the future generation of Welders
Stay up to date